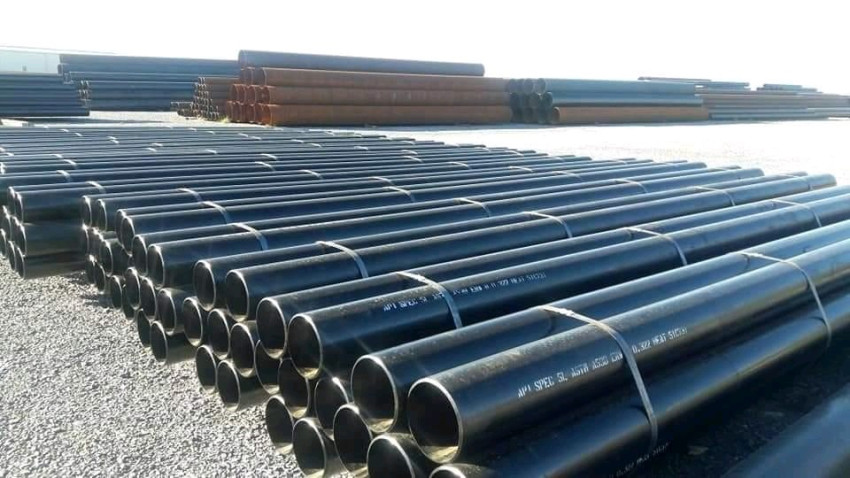
There are many factors affecting the straight seam high frequency welded steel pipe (ERW pipe), and these factors interact with each other. Only by mastering the quality control points of straight seam high frequency welded steel pipe can we better adjust them. So what are the main factors affecting high frequency welding?
1. Welding frequency
The high-frequency frequency will affect the uniformity of the current distribution inside the steel plate. When selecting the frequency of high-frequency welding, it is necessary to consider not only the depth of heat penetration, but also the proximity effect. Generally, the current frequency can be appropriately increased, which not only saves electric energy but also improves the quality of the weld and reduces the size of the heat-affected zone of the weld. In terms of welding efficiency, use a higher frequency as much as possible. 100kHz high-frequency current can penetrate ferritic steel 0.1mm, 400kHz can only penetrate 0.04mm, that is, the current density distribution on the surface of the steel plate, the latter is nearly 2.5 times higher than the former.
In production practice, the frequency of 350~450kHz can generally be selected when welding ordinary carbon steel materials. For welding alloy steel materials, when the plate thickness is more than 10mm, the frequency of 50~150kHz can be used, because the skin effect of chromium, zinc, copper, aluminum and other elements contained in alloy steel is different from that of steel.
2. Welding V-shaped corners
The size of the V-shaped angle has a direct impact on the welding quality. The proximity effect is significant when the V-shaped angle is small, which is beneficial to increase the welding speed, but the preheating section and melting section become longer, making the flashing process unstable, and deep pits and pinholes are easy to form after the lintel blasting, making it difficult to press. When the V-shaped angle is too large, the melting section becomes shorter and the flash is stable, but the proximity effect is weakened, the welding efficiency is significantly reduced, and the power consumption is increased. At the same time, when forming thin-walled steel pipes, if the V-shaped angle is too large, the edge of the pipe will be elongated, resulting in wavy wrinkles. In actual production, the V-shaped angle is generally adjusted within 2°~6°, thin-walled pipes generally use a smaller meeting angle; thick-walled pipes have slower welding speeds, and larger meeting angles are required for extrusion molding.
3. Welding power
If the power is too small, the heating of the groove of the tube billet is insufficient, and the welding temperature cannot be reached, which will cause unwelded defects such as virtual welding, desoldering, and clamping welding. When the power is too large, it will affect the welding stability, and the heating temperature of the groove surface of the tube blank is much higher than the temperature required for welding, resulting in serious spattering, pinholes, slag inclusions and other defects. This defect is called overburning defect. . The input power during high-frequency welding should be adjusted and determined according to the thickness of the pipe wall and the forming speed. Different forming methods, different unit equipment, and different material steel grades need to be summarized and optimized through practice.
In addition to the above factors, it also includes various factors such as welding speed, welding method, welding extrusion force, and impedance used. Only by mastering the quality control elements of these high-frequency welded pipes can better quality products be created.