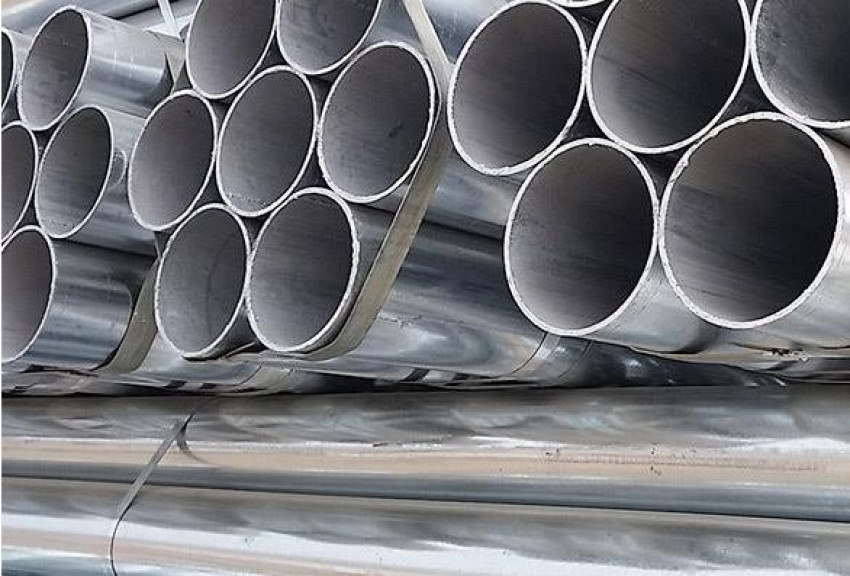
Welded steel tube refers to a steel pipe with seams on the surface that is welded after bending and deforming a steel strip or steel plate into a circular, square or other shape. The blanks used for welded steel pipes are steel plates or strips. According to different welding methods, it can be divided into arc welded pipe, high frequency resistance welded pipe (ERW pipe) or low frequency resistance welded pipe, gas welded pipe, furnace welded pipe, Bondi pipe, etc. The finished steel pipe often has defects such as inward folding and cracking, so the steel pipe should be inspected during the welding process
Inspection method of welded pipe welding quality: divided into pre-weld inspection, welding inspection, post-weld inspection
Here mainly introduces the post-weld inspection:
(1) Contents of post-weld inspection: appearance inspection, tightness test, and nondestructive inspection.
(2) Method of post-weld inspection
1. Appearance inspection
(1) Use a low-magnification magnifying glass or the naked eye to observe whether there are surface defects such as undercut, slag inclusions, pores, cracks, etc. on the weld surface.
(2) Use a welding inspection ruler to measure weld reinforcement, weld bumps, depressions, gaps, etc.
(3) Check whether the weldment is deformed.
2. Density test
(1) Leakage test with liquid: non-pressure equipment, directly contain liquid, and test the tightness of the weld.
(2) Air-tightness test: use compressed gas to pass into the container or pipeline, and apply foaming agent or soapy water to the outside of the weld to check whether there is any bubble leakage.
(3) Ammonia gas test: Ammonia gas is injected into one side of the weld, and a test paper soaked in phenolphthalein-alcohol and aqueous solution is pasted on the other side of the weld. If there is leakage, the test paper will turn red.
(4) Kerosene leak test: paint chalk powder water on one side of the weld, and brush kerosene on the other side of the weld after drying. If it leaks, the kerosene will leave an oily stain on the chalk.
(5) Helium test: Helium is injected into one side of the weld, and the tightness of the weld is measured by a helium leak detector on the other side of the weld.
(6) Vacuum box test: Apply foaming agent to the weld, and use a vacuum box to evacuate. If there is leakage, there will be bubbles. This test method is suitable for places where the other side of the weld is closed, such as the bottom weld of a storage tank.
3. Strength test
(1) The hydraulic strength test is usually carried out with water, and the test pressure is 1.25∽1.50 times the design pressure.
(2) Air pressure strength test uses gas as the medium to carry out the strength test, and the test pressure is 1.15∽1.20 times the design pressure
(2) Ultrasonic flaw detection (UT)
(3) Penetrant testing (PT)
(4) Magnetic flaw detection (MT)
(5) Ultrasonic time-of-flight diffraction (TOFD)
(6) Other detection methods include: metallographic analysis of large workpieces, ferrite content inspection, spectral analysis, hand-held hardness test, acoustic emission test, etc.